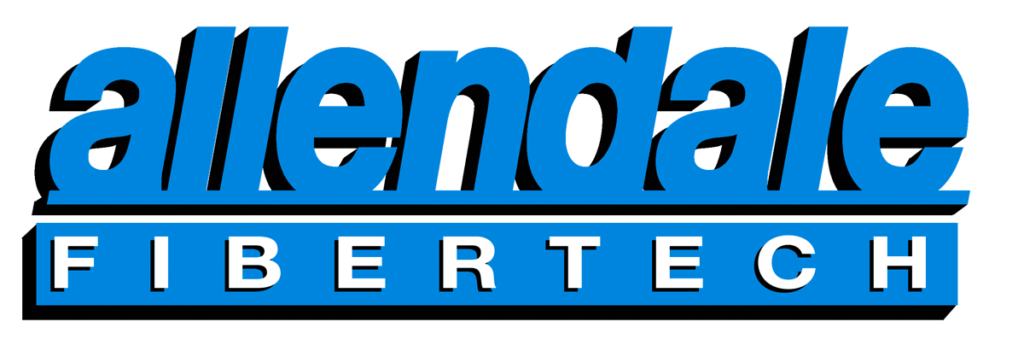
Fiber-Reinforced Plastics
Introduced over 50 years ago, composites are fiber-reinforced plastics used in a variety of products, applications and industries. While the term “composite” can apply to any combination of individual materials, Composites One focuses on fibers, primarily glass, that have been impregnated with a plastic resin matrix. Combining glass fibers with resin matrix results in composites that are strong, lightweight, corrosion-resistant and dimensionally stable. They also provide good design flexibility and high dielectric strength, and usually require lower tooling costs. Because of these advantages, composites are being used in a growing number of industries, such as recreational boating applications. Their tremendous strength-to-weight and design flexibility make them ideal in structural components for the transportation industry. High-strength lightweight premium composite materials such as carbon fiber and epoxies are being used for aerospace applications and in high performance sporting goods. Composites’ superior electrical insulating properties also make them ideal for appliances, tools and machinery. Tanks and pipes constructed with corrosion-resistant composites offer extended service life over those made with metals.
One of composites’ main advantages is how their components – glass fiber and resin matrix – complement each other. While thin glass fibers are quite strong, they are also susceptible to damage. Certain plastics are relatively weak, yet extremely versatile and tough. Combining these two components together, however, results in a material that is more useful than either is separately. With the right fiber, resin and manufacturing process, designers today can tailor composites to meet final product requirements that could not be met by using other materials. The key factors to consider are fiber, resin and filler, detailed below.
Glass-reinforced composites gain their strength from thin glass fibers set within their resin matrix. These strong, stiff fibers carry the load while the resin matrix spreads the load imposed on the composite. A wide variety of properties can be achieved by selecting the proper glass type, filament diameter, sizing chemistry and fiber forms (e.g., roving, fabric, etc.).
Fibers made primarily from silica-based glass containing several metal oxides offer excellent thermal and impact resistance, high tensile strength, good chemical resistance and outstanding insulating properties.
Fibers can also be produced from carbon, boron and aramid. While these materials offer higher tensile strength and are stiffer than glass, they cost significantly more. For that reason, carbon, boron and aramid are typically reserved for high-tech applications demanding exceptional fiber properties for which the customer is willing to pay a premium. An alternative is to use a hybrid fiber (combining an expensive fiber with a glass fiber), which improves overall performance yet costs less than using premium fibers alone.
E-glass is a popular fiber made primarily of silica oxide, along with oxides of aluminum, boron, calcium and other compounds. Named for its good electrical resistance, E-glass is strong yet low in cost, and accounts for over 90% of all glass fiber reinforcements, especially in aircraft radomes, antennae and applications where radio-signal transparency is desired. E-glass is also used extensively in computer circuit boards where stiffness and electrical resistance are required.
In addition to E-glass, several other types of glass can be used for composite reinforcement. The most popular are high-strength glass and corrosion-resistant glass.
High-strength glass, carbon or other advanced fibers are used in applications requiring greater strength and lower weight. High-strength glass is generally known as S-type glass in the United States, R-glass in Europe and T-glass in Japan. S-glass was originally developed for military applications in the 1960s, and a lower cost version, S-2 glass, was later developed for commercial applications.
High-strength glass has appreciably higher amounts of silica oxide, aluminum oxide and magnesium oxide than E-glass. S-2 glass is approximately 40-70% stronger than E-glass.
Corrosion-Resistant Glass Fiber
When glass fibers are exposed to water, they become eroded due to leaching.
To protect against water erosion, a moisture-resistant coating such as a silane compound is coated onto the fibers during manufacturing. Adding resin during composite formation provides additional protection. The result is corrosion-resistant glass (called C-glass).
Some types of glasses perform better than others when exposed to acids or bases. Both C-glass and S-2 glass offer good corrosion resistance when exposed to hydrochloric or sulfuric acid. E-glass and S-2 glass resist sodium carbonate solution (a base) better than C-glass.
Factors to consider when choosing glass type include thermal properties; fiber cost, type of manufacturing process being used, and forms of reinforcement, detailed below.
Thermal Properties
As temperatures increase, glass fibers lose tensile strength. C-glass performs poorly in high-temperature applications and should not be used for them. While E-glass and S-type glass lose about 50% of their tensile strength at 1000º F, their strength at high temperatures is still considered good.
Another temperature-related property to consider is the coefficient of thermal expansion (CTE). Fibers with a high CTE expand more as temperatures increase. S-type glass has a much lower CTE than either E-glass or C-glass. Having a similar CTE in both the fiber and resin prevents problems due to different thermal expansion rates.
Fiber Cost
Cost often is the deciding factor in choosing an appropriate glass type. It is priced based on quantity, filament diameter and other factors, bulk E-glass roving typically less expensive per pound, than C-glass. S-2 glass roving is typically more expensive. Product designers must weigh the benefits of advanced glass fibers against their higher cost in order to make the best selection for their application.
Fiber Manufacturing
Strength, corrosion-resistance and other properties result in part from the type of process used to manufacture the fibers. Processing complexity and material costs also determine glass reinforcement prices. During fiber production, bulk materials transform into web-like fans of delicate (and highly abrasive) glass filaments ranging from 3l5 to 24 micrometers in diameter. Silica sand accounts for more than 50% of the raw materials used. Varying raw materials and processing parameters can produce Glass types. For example, E-glass contains limestone, fluorspar, boric acid and clay.
Raw materials are mixed and then placed in a 2500º to 3000º F furnace for melting. Molten glass flows into one or more bushings containing hundreds (and sometimes thousands) of small orifices. It is immediately moved to a quench area where water and/or air quickly cool filaments.
In a typical glass fiber forming process, filaments are then pulled over a roller and coated with sizing. Traveling at high speed, each filament fan is pulled into a single strand and wound onto a tube. A strand typically contains hundreds of filaments and may contain more than 1000. After the spindle on the winder becomes full, the filament cake is transported to an oven where the sizing dries and cures. Fiber strands from the filament cake are used to produce roving and chopped fiberglass. Roving is also formed from multiple filament cakes placed into creels and then grouped together.
Sizing
Glass fiber could not be processed without sizing, which protects the fibers and helps bind them to the resin matrix. Lubricating oil in the sizing prevents high-speed machinery from damaging filament surfaces and causing lost tensile strength. Sizing chemical components protect fibers from moisture and provide conductivity so fibers are not attracted to electrically charged objects (human or machine). Sizing also has a coupling agent that improves bonding between the glass and resin matrix.
Sizing chemistry varies dramatically by application. For example, it can be formulated to improve fiber wet ability during resin impregnation, reducing composite manufacturing time. Coupling chemistry can also improve composite strength. Because of their competitive advantages, sizing formulations are proprietary for each manufacturer.
Forms of Reinforcements
Because they are extremely fragile, glass filaments are supplied in bundles called strands, roving or yarns. A strand is a collection of continuous filaments. A roving refers to a collection of untwisted strands or yarns. Yarns are collections of filaments or strands twisted together.
The most common materials used in composite manufacturing are roving, chopped fiber and fabrics. Roving is supplied on a weight basis with a specified filament diameter and yield, either as single-end (one continuous strand) or multi-end (numerous strands). Roving is also used to produce mat, woven fabrics, braids, knitted and hybrid fabrics, and other reinforcing materials. Mat, fabrics and braids keep fibers aligned prior to resin impregnation.
Mats
Available in chopped and continuous-strand, mat is non-woven fabrics that provide equal strength in all directions. Chopped-strand mat contains randomly distributed fibers cut in 1.5 to 2.5 inch lengths, held together with a chemical binder. Since the binder dissolves in styrene (a material contained in polyester and vinyl ester resins), chopped-strand mats conform easily to complex shapes. Providing low-cost plastic reinforcement, chopped-strand mat is primarily used in hand lay-up, continuous laminating and some closed molding applications.
Stronger than chopped-strand, continuous-strand mat is formed by swirling continuous strands of fiber onto a moving belt, finished with a chemical binder to hold fibers in place. Its open (non-dense) fiber arrangement accepts a high ratio of resin to fiber, resulting in a thick, smooth, resin-rich finish. Continuous-strand mat is primarily used in compression molding, resin transfer molding, pultrusion, fabricated platforms and stampable thermoplastic applications. These extremely lightweight mats are also used as “surfacing veils.”
Woven Fabrics
Woven fabrics are produced on looms in a wide variety of weights, weaves and widths. Bi-directional woven fabrics offer good strength in the 0- and 90-degree directions, and permit one laminate to be used for faster composite fabrication. They are made from fibers crimped as they pass over and under one another. Under tensile loading, these fibers try to straighten out, causing stress within the resin matrix system, so they are not as strong as fabrics with two separate laminates.
Several different weaves are used for bi-directional fabrics. In a plain weave, each fill yarn or roving alternately crosses over and under each warp fiber. Harness satin and basket weaves, in which the yarn or roving crosses over and under multiple warp fibers at a time, are more pliable and conform easily to curved surfaces. Due to its relatively coarse weave, woven roving wets quickly, is relatively inexpensive and results in a thick fabric used for heavy reinforcement, especially in hand lay-up operations. Exceptionally fine fiberglass fabrics are used for reinforcing printed circuit boards.
Hybrid fabrics are made by combining different types of glass and strand compositions together, such as using high-strength S-type glass strands or small diameter filaments in the longitudinal direction and less costly strands woven across the fabric. Stitching woven and mat fabrics may also create hybrids.
Knitted Fabrics
Knitted fabrics are created by placing yarns atop one another in practically any arrangement and stitching them together. Orienting all strands in one direction, for example, results in a fabric with greater flexibility. Placing the yarns on top of, rather than over and under, each other, makes greater use of their inherent strength. Since they have no crimped fibers, knitted fabrics are more pliable than woven.
Due to the wide variety of yarn orientations and fabric weights, knitted fabrics are tailored to individual customer requirements. They are generally not available in lightweight versions.
Braided Fabrics
Compared to woven, braided fabric has greater strength per weight, but is more expensive because of its complex manufacturing process. Manufacturing costs have decreased, however, making braided fabrics more cost-competitive. Their strength comes from intertwining three or more yarns without any two yarns being twisted around each other, continuously woven on the bias so that at least one axial yarn is not crimped. This arrangement distributes the load efficiently throughout the braid.
Braids come in flat or tubular configurations. Flat braids are used for selective reinforcement, such as strengthening specific areas in pultruded parts. Tubular braid can be pultruded over a mandrel, producing hollow cross-sections for use in windsurfer masts, lamp and utility poles, and other parts.
Matrix resins bind glass-reinforcing fibers together, protecting them from impact and the environment. Glass fiber properties such as strength dominate in continuously reinforced composites. When glass is used as a discontinuous reinforcement, resin properties dominate and are enhanced by the glass.
Polymer matrix resins fall into two categories: thermoset and thermoplastic. The difference is in their chemistry. Thermoset resin is chemically comprised of molecular chains that crosslink during the cure reaction (set off by heat, catalyst, or both) and “set” into a final rigid form. Molecular chains in thermoplastic resin are processed at higher temperatures and remain “plastic,” or capable of being reheated and reshaped. While the tradeoffs between thermosets and thermoplastics have been debated extensively, engineers will find that material suppliers will tailor matrix resin formulations best for their application.
With their track record of performance, thermosets have become the matrix of choice in continuously reinforced glass fiber composites and plastic parts made with glass filler. Especially popular are unsaturated polyester resins, which are relatively inexpensive, easy to handle, and have good mechanical, electrical and chemical resistance. Polyesters can be used in multiple fabrication processes, from spray-up boats and spas to compression molding and resin transfer molding (RTM) for making auto body parts, as well as injection molded electrical components. Polyester is also the primary resin matrix in bulk molding compounds (BMC) and sheet molding compounds (SMC) used in compression molding.
Adding glycol, acid, reactive monomers (commonly styrene) and other materials during forming can enhance polyester’s properties for specific applications. For example, additives and fillers are used to make polyester resin more chemical or corrosion-resistant, fire retardant, shrink-resistant and thermally stable, as well as capable of withstanding weather conditions.
Polyesters are named for their ingredients, such as orthopolyesters (utilizing orthophthalic acid), isopolyesters (resins containing isophthalic acid for superior chemical and thermal resistance), and terephthalic resins (formulated with terephthalic acids for improved toughness).
Thermoset polyesters cure in an exothermic manner, in that the cross-linking process releases heat as it occurs. By balancing inhibitors, catalysts and accelerators, fabricators can control this cure profile in terms of shelf life, pot life, gel time, cure temperature and viscosity. Also available are new low-profile polyester formulations that can be molded at low pressures (300 psi) and then used in SMC applications for large automotive parts requiring a Class A finish.
Special polyester resin formulations have greater impact and abrasion resistance and better surface appearance. Known as gel coats, these resins are applied to a mold surface and gelled before lay-up of reinforcements and matrix resins.
Vinyl esters cost more than polyesters but are used in many of the same applications. Their performance surpasses polyesters in chemically corrosive environments (such as filament wound glass/vinyl ester chemical tanks) and structural laminates requiring high moisture resistance (such as boat manufacturing).
Another popular thermoset is epoxy resin, which is used in structural aerospace applications, particularly with carbon fibers, and electronics applications such as printed circuit boards. While epoxies are generally more expensive than polyesters, they have less shrinkage and higher strength/stiffness at moderate temperatures. They are also corrosion-resistant to solvents, alkalis, and some acids. As with polyesters, epoxy resins can be used in most composite manufacturing processes. They are available in different formulations to provide desired properties and optimize the manufacturing process.
The most common types are diglycidyl ether of biphenyl A (DGEBPA) and the epoxy novolacs (comprised of glycidyl ethers of cresol novolac, phenolic novolac, or biphenyl A novolac). Cross-linking depends upon the hardener system (commonly aromatic or aliphatic amines or acid anhydrides) used. Compared to polyesters, epoxy resins take longer to cure and have no by-products.
Epoxies with lower density cross linking have improved toughness and shrinkage, while those with higher density cross linking have better chemical resistance and increased heat-distortion temperature (HDT).
Resin properties can also be tailored by using different cure system hardeners. Aliphatic amines allow formulations to cure at room temperature, aromatic amines enhance chemical resistance and result in more rigid final parts, and acid anhydride hardeners offer superior electrical properties.
Phenolic resins have proven superior in high temperature applications such as rocket nozzles for many years. Previously available in prepreg form (requiring autoclave cure) or as injection molding compounds, it now comes in a new, low viscosity version that is easier to process and practical for a variety of applications including those with low volumes.
Phenolics are particularly useful in composite parts that must meet smoke emission, combustion and toxicity requirements. They can be found in mass transit, construction, mining and tunneling applications, as well as in flooring and interior cabin liners of passenger airplanes. In the automotive industry, glass-reinforced phenolic heat shields have been tested to retain their tensile strength up to 480º F, with short spikes at higher temperatures. With their reduced cost, lightweight and other advantages, glass-reinforced phenolics have replaced metal in automotive powertrain components.
Although difficult to process, phenolics offer low density, good thermal insulation, outstanding durability and ease of formability to complex contours (when impregnated with fabric). Colored phenolics and complementary acrylic-based gel coat formulations meet additional applications, particularly in mass transit.
Both polyurethane and polyamide can be formulated into thermoset or thermoplastic resins. Thermoset polyurethane enhances the rigidity of automotive bumper fascias through reaction injection molding (RIM), a process where reactive resins are injectedunder high pressure into a mold. Capable of performing at temperatures up to 700º F, thermoset polyamides are mainly used for advanced composite matrices. Thermoplastic polyamides readily release volatiles under heat and pressure, resulting in more void-free parts.
With their high electrical properties and chemical resistance, polybutadiene resins have been successfully used in thin-walled glass-reinforced radomes as an alternative to E-glass/epoxy composites.
While thermosets are more widely used, thermoplastic resins are available in a significantly wider range of matrix choices. Higher in cost, they are also high-performance, withstanding temperatures up to 400º F and beyond. Besides elevated temperature performance, thermoplastic resins have better toughness/damage resistance and higher compressive strength. In advanced composites, they also exhibit high vibrational damping, viscoelasticity (important in failure resistance) and low CTE. In prepreg form, thermoplastics do not require refrigeration and have extended shelf life. The downside is that they require processing near 600º F or above.
Compared to thermosets, thermoplastics used with long glass fiber and milled/chopped glass fiber as filler (particularly injection molded plastic parts) or in chopped-strand mat offer greater impact resistance and reduced hygroscopy (readiness to absorb moisture). They also extend processing options (with thermoforming, for example) and take less time to process than thermosets.
Based on cost and properties, there are two categories of thermoplastics: commodity resins and engineering resins.
The most common commodity thermoplastic resins are polyethylene, polystyrene, polypropylene and thermoplastic polyesters (PET, PBT). Melt flow and density options, enhanced impact resistance and relative ease of processing characterize them.
Engineering thermoplastics include acrylonitrile butadiene styrene (ABS), acetal, nylon (semicrystalline polyamide), polycarbonate (PC), polyvinyl chloride (PVC), and polysulfone resins. These thermoplastics work well in automotive applications such as fuel system components and engine air intake manifolds.
Thermoplastics reinforced with non-continuous fiberglass are used to manufacture a wide range of consumer, commercial and light industrial products. Because of its high processing temperatures, thermoplastics are not cost-effective in hand lay-up and spray-up fabrication projects, unless high-performance mechanical and physical properties are demanded.
With automated processes such as pultrusion and filament winding, equipment designed for thermoset processing must first be modified in order to fabricate continuous fiberglass reinforced thermoplastics. Successful approaches have been developed and demonstrated, but are not widely used today. Most FRP manufacturing processes use thermoset resins.
Fillers, such as gypsum, calcium carbonate (limestone), kaolin (clay) and alumina trihydrate are often used in composites to enhance performance and reduce costs. Compared to resin and reinforcements, they are inexpensive. Depending on the material used, fillers can improve smoke and fire resistance, mechanical strength, water resistance, surface smoothness and performance characteristics.
Core Materials are used in sandwich composite construction to add stiffness and strength to a product with minimal increase in weight. A skin of reinforced laminate is applied to both sides of the core material. The skins take the loading while the core is only required to keep the skin a specified distance apart.
By increasing the core thickness, you geometrically increase the stiffness of the core structure.
More to read:
APPLICATIONS OF FIBER REINFORCED
POLYMER COMPOSITES: https://allendalefibertech.com/wp-content/uploads/2023/02/FRP-Applications.pdf